84 Engineering is an Australian-made and owned company that specializes in the production of belt grinders. This company has a strong reputation for producing high-quality grinding tools that are used by professionals in a variety of industries. With a focus on innovation and attention to detail, 84 Engineering has become a trusted name in the world of grinding and metalworking. Whether you are a professional craftsman, knife maker, a hobbyist, or anyone in between, 84 Engineering has a belt grinder that is right for you.
We were lucky enough to visit the 84 Engineering facility in Cooma, NSW, a beautiful town at the doorway to the Snowy Mountains. Upon arrival, we were greeted by our host, Ewan Gibson, and the shop dog, Jax. We were also introduced to the rest of the team, including his wife Sarah Gibson. It was a pleasure to meet everyone and see the inner workings of the facility.
Ewan Gibson
Jax The Shop Dog
On our tour we were shown the machinery used to produce the high quality parts, one of the machines was the DMG MORI NLX 2000 | 500. The NLX 2000 is a high-rigidity, high-precision turning centre with a standard chuck size of 8 inches, handling various workpieces. The model is equipped with high turning capabilities supported by a robust bed, and superb milling performance with the matured BMT (Built-in-Motor Turret).
The space-saving design enables an easy establishment of automation systems. The model demonstrates outstanding abilities in a wide range of fields including the automotive parts industry producing mass-production parts and the aircraft industry requiring ultra-precision quality.
NLX 2000 CNC
The NLX is a machine used by 84 Engineering to produce the Contact and Drive wheels used on all of its grinding machines. In addition to its primary function, the NLX also has the ability to engrave the 84 Engineering insignia on the face of the wheels.
The CNC, or computer numerical control, machine uses an automated robot to load billet aluminium into the chuck for milling. Once the milling is complete, the finished product is stacked onto a receiving platform, allowing the machine to run without human intervention. This technology allows 84 Engineering to efficiently produce high-quality products.
Aluminium Blank in CNC Chuck
Aluminium Blank Being Machined
Aluminium Blanks In Stacks, Some Finished And Some In Raw State
In the back corner of the 84 Engineering facility, there is a Japanese-made Hamatu 20 manual lathe that is used for prototyping and other special projects. In addition to this machine, 84 Engineering also uses three CNC machines for different stages of production. One of these machines is an Okuma CNC Vertical Machining Centre Model Genos M560-V-e S15. This machine is primarily used for milling smaller aluminium brackets and rectangle tooling arms that make up the grinder.
Japanese-made Hamatu 20 Manual Lathe
During our visit, we were able to watch Liam load up some billet aluminium and run a program on the CNC machine to see how the process works. It was fascinating to see the machine in action and to learn more about the manufacturing process at 84 Engineering.
Liam Running The Okuma CNC Vertical Machining
The team at 84 Engineering has a strict quality control process in place to ensure that only the best finished parts move on to assembly. This careful attention to detail helps the company maintain its reputation for producing high-quality products.
Powder coating is a popular finishing process used in many industries, including manufacturing. It involves applying a dry powder coating material to a surface, which is then cured and adhered to the surface using heat. This process results in a smooth, durable, and attractive finish that is resistant to chipping, scratching, and other forms of damage. At 84 Engineering, the powder coating material used is a Teflon powder, which offers additional benefits such as resistance to heat and chemical damage. Powder coating is a popular choice because it is environmentally friendly, cost-effective, and offers a wide range of colour options. The powder coating process is handled by a local business and the finished parts are returned in crates ready for assembly.
Grinder Parts Ready For Powder Coating
Shop Master Parts Ready To Powder Coat
In a separate room, Mark, the welding master, assembles everything from the tool rests to the bodies of the Gibson grinders. This is also where the team tests out new parts on the shop grinders. This room is an important part of 84 Engineering's manufacturing process, as it allows the company to create high-quality products and experiment with new ideas.
Mark The Welding Master At Work
Gibson 72 Parts Ready For Welding
Wheel assembly is done entirely in-house at 84 Engineering. This includes the manufacturing of the polyurethane, casting it in moulds, and resurfacing the wheels for optimal size and consistency. By handling every step of the process in-house, the company can maintain control over the quality of its products.
84 Engineering has developed a proprietary process for manufacturing its Polyurethane wheels, which has been yielding impressive results. After the wheels are made, they are stacked and quality checked before moving on to assembly and packaging. This careful attention to detail ensures that each product meets the company's high standards.
Wheel Ready For Polyurethane
Wheels Cast And Ready For Finishing
Wheel Ready For Surfacing
Upstairs, you can find the packaging operation for the grinders and parts/accessories. The heart of this operation is the ESKO Kongsberg X. This machine has the ability to cut out any design in cardboard, including crease lines for folding. This is a key part of 84 Engineering's manufacturing process.
Raife Aka Master box maker, designs all the packaging and ensures the end product arrives to the consumer in top condition.
Raife Aka Master Box Maker
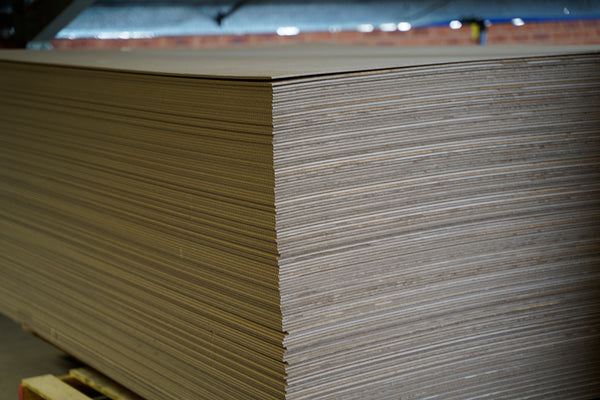
Raw Card Board Ready For Cutting
Away from the production side of the 84 Engineering facility is the storage and assembly area. This is where finished products are stored and prepared for dispatch to customers. We had the opportunity to meet Kyle Rowling, who works in this area. Kyle is an experienced stuntman and actor who has worked on several high-profile films, including Star Wars: Episode II Attack of the Clones and Star Wars: Episode III Revenge of the Sith. He has also appeared on screen in several roles, including as Joclad Danva in Attack of the Clones.
After a successful career in the film industry, Kyle wanted a change of scenery and joined the 84 Engineering team. At the time of our visit, he was working on assembling some parts for dispatch. It was interesting to hear about his background and how he came to be part of the 84 Engineering family.
Jedi Master Kyle Preparing Floor Stands
Each packing and assembly table at the 84 Engineering facility is dedicated to a specific component of the grinder. The workspace is color-coded to match the corresponding assembly tools, which helps with speed and efficiency. This system also helps prevent user mistakes, such as adding incorrect washers and bolts to a component.
In addition to the color-coded workspace, there are detailed assembly instructions available so that any member of the team can jump in and assemble the components. This is similar to an IKEA assembly manual, and it allows for flexibility and efficient production.
2x Assembly Stations
Pedestal Stand Assembly Station SM-HAPS
84 Engineering keeps all of its externally purchased components, such as Japanese bearings, Socket Head bolts, and washers, in labelled tubs for easy recognition and inventory management. This organization system helps the company maintain accurate stock levels and ensures that the necessary components are readily available when needed. It also makes it easier for the team to find the components they need, which helps with efficiency and productivity.
Storage Tubs For Small Bearings And Bolts
At 84 Engineering, great care is taken to ensure that the Japanese bearings used in the company's products are of the highest quality. To fit the bearings into the aluminium bodies, a manual bearing press is used. This allows the team to carefully and accurately seat the bearings, ensuring that they are properly aligned and functioning properly. Once the bearings are in place, they are checked to ensure that they meet the company's high standards. This attention to detail helps ensure that the finished products are of the highest quality and will perform reliably for the customer.
Bearing Press
Bearing Being Pressed Into Contact Wheel
On the manufacturing floor, there is a separate room where all of the VFD, or variable frequency drive, components are kept and assembled onto Techtop motors. The VFD is a key component of the grinding machines produced by 84 Engineering, as it allows the machine to operate at a range of speeds, depending on the needs of the user. This room is an important part of the manufacturing process, as it ensures that the VFD components are properly assembled and integrated into the final product.
VFD Assembly And Storage
Once the parts are fully assembled, they are packaged into the appropriate boxes, labelled, and sealed. This preparation is necessary to ensure that the products are ready for dispatch to the customer. The team at 84 Engineering takes care to properly label and seal each box, so the customer knows what they are receiving and the products are protected during transportation.
Products Ready For Dispatch
On our tour, we had the pleasure of meeting Shane, who manages the website and social media for 84 Engineering. It was interesting to learn about this aspect of the business and how it helps the company connect with its customers and promote its products. Shane's work is an important part of the company's overall operations and helps 84 Engineering maintain a strong online presence.
Shane, Ewan, Raife
If you want to support an Australian business that produces some of the highest quality grinding tools in the world, consider 84 Engineering. This company has a great reputation and a family-like atmosphere that makes for a positive experience.
The team at 84 Engineering is dedicated to innovation and is always working on new and improved parts and products. This commitment to progress allows the company to stay at the forefront of the grinding and metalworking industry and offer its customers the best possible products. Whether it is developing a new type of grinding wheel or refining an existing product, the team at 84 Engineering is constantly working to push the boundaries of what is possible. This dedication to innovation is one of the many reasons that 84 Engineering is a trusted name in the world of grinding.
If you are in the market for a high-quality belt grinder, look no further than the Shop Mate and Shop Master grinders from 84 Engineering. These grinders are designed and manufactured in Australia to the highest standards, and they are built to last. In addition to the grinders themselves, 84 Engineering also offers a range of accessories, including grinding wheels, tool rests, and more. Don't miss out on the opportunity to own a premium belt grinder - purchase a Shop Mate or Shop Master today and experience the quality and performance that sets 84 Engineering apart.
Thank you to the team at 84 Engineering for the great experience and for being such wonderful hosts.